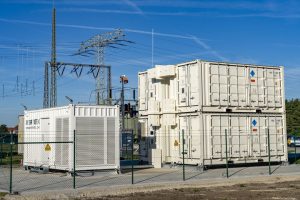
“The stationary energy storage system is another step towards increased sustainability in battery production for electric vehicles,” said company v-p of battery metals Daniel Schönfelder. “It means that we can use renewable energies almost around the clock, for instance for our manufacturing of cathode materials or for the production of black mass in the recycling of old batteries for electric vehicles in Schwarzheide.”
Expected life is 20 years or 7,300 cycles.
The batteries are made by NGK Insulators, distributed in this case by fellow BASF subsidiary BASF Stationary Energy Storage.
Sodium-sulphur is a high-temperature technology, with the cells needing to run at between 300 and 340°C.
The batteries are insulated, and modelled on a 20ft shipping container – four were required for this installation.
Operation is over ambients of -20 to +45°C (-40 to +55°C optional), supported by air conditioning for the control electronics container and up to 33kW of auxiliary heating for each battery container.
Inside the batteries, each NGK cell measure 90mm in diameter and 500mm long.
Nominal cell voltage is 2V and densities are 367Wh/litre, 222Wh/kg and 36W/kg.
“They have so far been installed in over 250 locations around the world and have a stable operational track record of more than 20 years,” said NGK. They “have obtained the certification based on stationary storage battery safety standard UL 1973 [cell and module level] and a test report based on UL 9540A ,which is to verify batteries and storage battery systems fire risk”.
With energy density and power, plus the problem of having to run at 300°C, it doesn’t seem like a big deal… what’s the point anyway? Price?