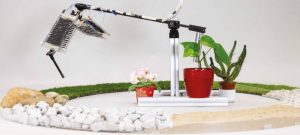
This sort of electricity-to-movement transducer uses a liquid-filled bag with electrodes on opposite faces. A high potential difference across the electrodes pulls them together, squashing the liquid out of the way – and that action can be exploited in various physical ways.
In this case (diagram left), the black electrodes pull together, slightly elongating their end of each cell. This pushes the yellow liquid up the other end of each cell, pushing it into a ball shape (or sausage shape, in the wide cells actually used), considerably shortening that end.
The result that each cell shortens somewhat in its actuated state, and the whole assembly can pull like a muscle.
Using four of these, used in opposing pairs like human leg muscles, the team built a leg from carbon fibre poles and hinges – suspended from a frame in the photos.
Various control schemes were tried, including using feedback from angle sensors in the joints, and capacitively sensing the actuation electrodes.
Precise movements were available with feedback, and useful behaviour was available without feedback – even simple open-loop voltage level drive allowed the leg to shift weight up and down as well as making it jump, and imparted a natural tuneable soft landing action which worked to its advantage when hopping through varied terrain (top photo).
“Adapting to the terrain is a key aspect,” explained researcher Toshihiko Fukushima. “When a person lands after jumping into the air, they don’t have to think in advance about whether they should bend their knees at a 90° or a 70° angle.”
An electromagnetic leg, with joints replaced by electromagnetic rotary actuators, was made for comparison.
While this had some advantages, it lost badly when having to hold a static position – the electro-hydraulic leg needed only 1.2% of the energy consumed by the electromagnetic leg.
However, said team leader Robert Katzschmann, electro-hydraulic actuators have their limitations.
“The leg is currently attached to a rod, jumps in circles and can’t yet move freely,” he said. “Compared to walking robots with electric motors, our system is limited.”
That said, “if we combine the robotic leg in a quadruped robot or a humanoid robot with two legs, maybe one day, when it is battery-powered, we can deploy it as a rescue robot”.
And, Katzschmann added, they offer advantages over standard electric motors in grippers, where the movements have to be adjusted depending on whether a ball, an egg or a tomato is being lifted.
Max Planck ETH Center for Learning Systems is a partnership between ETH Zurich and the Max Planck Institute for Intelligent Systems (MPI-IS), extablished in 2015.
Read more in the Nature Communications paper ‘Electrohydraulic musculoskeletal robotic leg for agile, adaptive, yet energy-efficient locomotion‘ – which can be read in full without payment.
Images:
Thomas Buchner ETH Zurich
Toshihiko Fukushima MPI-IS
Wolfram Scheible MPI-IS