One of the key areas where a real difference to increasing consumer appeal can be made is an electric vehicle’s (EV) energy storage reserves. The battery pack is an essential element of any EV design and one of the biggest contributors to the overall bill of materials. Technological innovation is needed to extend the range of the EV and lifetime of the battery.
Formats for common battery cells
Cells serve as the primary building blocks for energy storage in EVs. These cells are organised into modules, with numerous modules forming a battery pack. There are three main cell formats used in EV battery packs, see Figure 1.
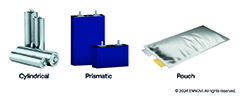
Figure 1: The three popular EV battery cell formats
Cylindrical, prismatic and pouch
Cells that are cylindrical in shape help to reduce stress and internal pressures while preventing swelling. Currently, these are the smallest battery cells in use. As a result, more cells are needed to fill a module, necessitating an increased number of connections. Furthermore, due to their design, when packed into a module, there is dead space between the cells, wasting important real estate.
Prismatic cells have a rectangular shape and are contained in rigid casings. They are generally larger than cylindrical cells. A key advantage over cylindrical cells is that fewer connections are required, resulting in less welding work. This makes them suitable for the streamlined EV production procedures that OEMs are keen to employ.
Pouch (also known as polymer) cells are enclosed in a laminated foil pouch rather than the rigid casing that prismatic cells use. This flexibility allows for a greater package density. They are prone to swelling, however, and are more vulnerable to punctures or injury, necessitating a strong protective case construction.
Advances in battery pack design
OEMs want to store more electrical energy within the battery pack to enable the EV to travel greater distances between charges. One way of doing this is to increase the cell density. Modern packs typically consist of only a few modules, reduced from the earlier generation of battery packs that could have as many as 48. This reduction not only improves battery storage capacity by decreasing redundant space, but it also simplifies battery pack design and lowers production costs.
Eventually this evolution will lead to the use of cell-to-pack or cell-to-chassis arrangements, which will eliminate modules completely. This development will allow for more storage capacity and lighter battery packs, but implementation must be carefully weighed against safety concerns regarding high cell density packs.
Optimising the cell contacting system
The way in which the cells are connected within the modules has a considerable impact on system performance, safety and manufacturing costs. To be effective for EV deployment, the selected cell contacting system must possess several qualities.
Conventional cell contacting system assemblies are often made from aluminium-based alloys, which are less expensive and lighter than copper-based alloys. In the case of certain cell types they can be highly complex, needing many layer constructions and having parts with varying thicknesses. The changes in metal thickness and how the current travels through the connection result in a lack of uniformity in the current density distribution, as well as the heat distribution.
Variations in current distribution can generate hotspots, placing unwanted stresses on the battery cells and, thereby, shortening their operational lives. Since a battery is only as good as the least effective of its cells, once these start to become dysfunctional it will not be long before the whole pack needs to be replaced. This replacement will have a heavy associated expense, and so stretching the working lifespan of the battery pack is a top priority. While there are cell balancing methods that can compensate for poorly performing or poorly connected cells, their effectiveness is limited, especially as the number of cells per module increases.
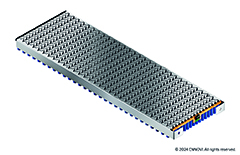
Figure 2: A battery pack assembly featuring Ennovi’s cell contacting system
One proposed solution that can support EV battery modules is a cell contacting system made up of both cylindrical and prismatic cells. Cell attachment is via laser welding, which is claimed to ensure that current density remains consistent across all cells to which it is attached (see Figure 2). It also means individual battery cells are subjected to significantly less stress, allowing battery packs to operate for much longer.
Through precision engineering, the thickness of the cell contacting system can be adjusted in specific areas, such as reducing material in the cell tabs and increasing it in the main current paths. This thinner profile, with fewer layers, creates additional space for energy storage. Moreover, less metal conductor material is required, resulting in reduced heat generation that needs to be dissipated.
Inadequate heat dissipation places greater stress on battery cells, accelerating their deterioration and leading to premature end-of-life scenarios. While alternative cell contacting systems may address the heat issue by adding extra insulation, this would only add to the bill of material costs.
Alternatively, the only other thermal management option would be to enhance the cooling system. This could involve either specifying a larger cooling system, occupying more space, or running it with higher power consumption. Either approach would result in increased electricity usage, reducing available battery charge for propulsion and limiting the vehicle’s range.
In this case, the patented U-Turn technology achieves a significantly more uniform distribution of current density, effectively reducing the formation of hot spots within the module. Conventional cell contacting systems require an additional busbar for taking the current back to the negative terminal, which requires an extra layer that can generate heat (see Figure 3).
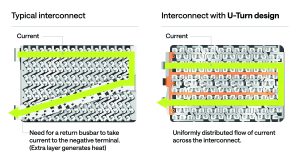
Figure 3: Comparison between the current dispersion in a conventional EV cell contacting system and one using U-Turn technology
The proprietary technology is claimed to organise energy flow more efficiently from the positive to the negative terminal and is streamlined (Figure 4). It requires only a single conductor layer, enhancing heat dissipation. The technology is also fully scalable, accommodating modules and battery packs of any size to meet the high-volume manufacturing demands of the automotive industry.
Extended lifespan
It is evident that ensuring a long-lasting battery resource is crucial to make EV models appealing to consumers. For this, maximising the lifespan of individual cells within the battery pack is paramount. The uneven current and heat distribution seen in existing cell contacting systems accelerate cell deterioration and unnecessarily raise production and material costs.
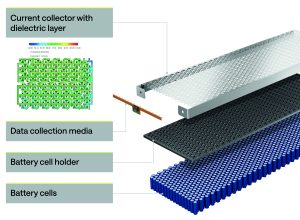
Figure 4: An exploded view of Ennovi’s proprietary U-Turn design in an EV battery cell contacting system
It has been shown that a streamlined interconnect design that allows more even current spread across the cells and augments heat dissipation could mitigate the emergence of hotspots. As a result, cells will all age at approximately equal rates and the battery pack will have an extended lifespan.
This approach offers other advantages in terms of ease of implementation and increased energy storage density, which, in turn, extends the distance that the EV can travel before needing recharging.