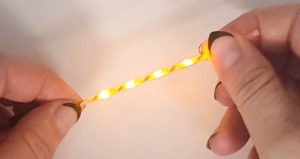
To make the electronic fibre, a long thin flexible PCB is helically wound along, and bonded to, the elastomer core, with its components facing inwards.
“The basic idea has been around for centuries – it’s the same concept as taking a metal wire and making it stretchy by winding it into a spring.,” said Nottingham medical engineer Jessica Stanley. “While helices have already been used in stretchable electronic devices, up to now they have only been used as interconnects or single components. What sets our work apart is that strips of flexible circuitry containing circuits more complex than a single wire or printed component are wound into a helix so that the entire circuit can stretch.”
The research team has modelled and made prototypes with PCBs of different widths and helix angles around fibres of different diameters and physical properties, bonded with multiple adhesives.
It has settled on cores of around 4mm diameter and winding angles in the region of 30° for the best compromise between stretch and durability – which is counted in thousands of stretching cycles without damage, and multiple wash cycles in fabric.
Hollow transparent silicone tubing worked as a core for a circuit with multiple LEDs (see photo), with the hollow centre squashing to accommodate the height of the LEDs. Lower profile components such as thermistors could be wrapped around solid rubber cores.
Flexible cyanoacrylate adhesive worked as a bonding medium in many circumstances.
“We have been able to show the potential for a new form of 3D helical strip for embedded electronics in e-textiles,” said fellow researcher electronic engineer Yang Wei. “We have defined the design, developed prototypes, performed mechanical testing and validated the functionality of the concept. This opens up a range of possibilities for e-textiles in healthcare and sports settings.”
Industry partner Kymira was involved in the project, which has resulted in a patent.
Scientific Reports has published the findings as ‘Stretchable electronic strips for electronic textiles enabled by 3D helical structure‘, which can be read in full without payment and describes what worked, what didn’t, and the associated failure modes.