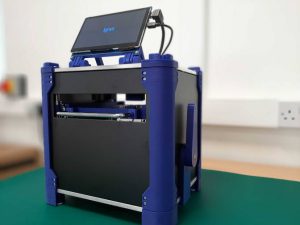
“For high volume products, there are conventional ways of arranging tests but these are often too expensive and too slow for the start-up community or low volume manufacturers to benefit from,” according to the company. “We’ve developed the Ignys series of production test fixtures to level the disparity between high volume deeper pocket manufacturers, and smaller nimble start-ups and SMEs.”
To keep costs low and speed turn-around, each jig is a compact portable unit made from a mixture of standard parts, including a Raspberry Pi and off-the-shelf mechanical components, and 3d printed custom parts specific to the assembly-under-test.
The underlying frame consists of two square flat plates joined by rods (photo left, corner covers removed).
They are portable and have plastic parts – are they robust?
“There are heavy-gauge aluminium top and bottom plates to give it rigidity and some weight, then most of the moving parts run with metal bearings on metal rods,” company MD Richard Fletcher told Electronics Weekly – the linear bearings are just visible in the left photo.
The assembly to be tested is placed in a custom pull-out draw (photo right), pushed in, then pulled down onto a bed-of-nails for electrical connection – the holder for the pogo pins is also a bespoke 3d print.
Black plastic sides finish off the assembly.
Ignys creates its own interface HATs (add-on adaptor boards) for the on-board Raspberry Pi, and appropriate test software is written in-house in Linux. The Raspberry Pi also drives the built-in display.