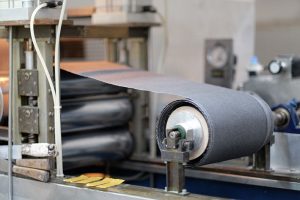
The ingredients are cellulose, conductive polymers and bio-based charcoal from coconuts, and the result is durable, electrically conductive and has a large surface area structure that can bind energy-storing materials.
Update: Supercapacitors with cellulose active material on paper substrates
“Our goal is to use the paper material to build prototype supercapacitors before the end of the year”, said Jesper Edberg of at partner research agency RISE. “We also plan to add electrochemically active materials that will enable the paper to be used in battery applications. Then the energy density would increase significantly because batteries can store more energy than ultracapacitors. Our previously research has also shown that such batteries can be manufactured from forest-based materials.”
In a proof-of-concept with industrial partners Agfa and Ahlstrom-Munksjö, the Center set out to prove that the electrode paper could be made on a large scale with conventional techniques.
“It was manufactured in regular paper machines, with several paper rolls produced, ten of meters each,” according to the Center. “Testing showed that the paper has as efficient energy storage capacity as conventional supercapacitors.”
To make conventional paper, elongated fibres are dispersed in water, a homogeneous layer is made, then the water is removed. Cellulose is what binds the material together and turns it into a paper.
For the electronic paper, its fibres must first be coated with electroactive components (conductive polymers and the coconut charcoal) and these active components must remain attached as the fibres are formed into a network. Just the right amount of active ingredient has to be incorporated, as too much will make the paper fall apart.
In the continuous process, a wet mixture of all the components is distributed on a fine wire mesh, through which water is sucked out by vacuum (left). This layer is pressed to remove more water, also strengthening the network, then heat is used to evaporate the remaining water before the paper is rolled (above).
As well as RISE, Digital Cellulose Center is working with Swedish researching institute KTH and Linköping University on this project. Agfa supplied electrically conductive polymers and Ahlstrom-Munksjö manages a pilot plant in France.