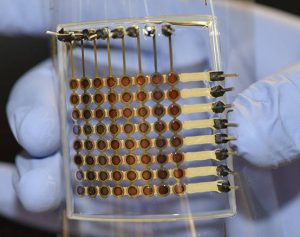
To prove it can be done, researchers at the University of Minnesota Twin Cities has 3D printed everything in a flexible OLED display, except for the plastic sheet it was printed on.
The 64 pixel display is around 40mm across
“OLED displays are usually produced in big, expensive, ultra-clean fabrication facilities,” said Minnesota professor Michael McAlpine. “We wanted to see if we could condense all of that down and print an OLED display on our table-top 3D printer, which was custom built.”
The team combined two types of printing to build the six-layer device: electrodes, interconnects, insulation and encapsulation were all extrusion printed, swapping to a spray nozzle to accurately control the thickness of thin active layers.
Depositing 1mm liquid metal beads, which will later be squashed into the correct shape by their own oxide films
“The device exhibited a relatively stable emission over the 2,000 bending cycles, suggesting that fully 3D printed OLEDs can potentially be used for applications in soft electronics and wearable devices,” said fellow engineer Ruitao Su, now at MIT.
Starting with the PET substrate, the team printed:
Silver nanoparticle ink for bottom conductors and to define the pixel outlines
- PEDOT:PSS conductive polymer (right) to improve current injection into the active layer
- MDMO-PPV electroluminescent polymer as an active layer in which carriers recombine
- Silicone-based insulation to separate the bottom conductors from the top conductors, exposing only the active OLED areas to the cathode
- An array of eutectic gallium-indium alloy droplets for the cathode
- Silver conductors
Encapsulation in flexible polydimethylsiloxane protected the display.
“The nice part about our research is that the manufacturing is all built in, so we’re not talking 20 years out with some pie-in-the-sky vision,” said McAlpine. “This is something that we actually manufactured in the lab, and it is not hard to imagine that you could translate this to printing all kinds of displays ourselves at home or on the go within just a few years, on a small portable printer.”
The work is published at “3D printed flexible organic light-emitting diode displays” in Science Advances – full paper available without payment.
To get some idea of the sophistication involved, according to the paper:
To “create stable polymer-metal junctions, we leveraged the viscoelasticity of the oxide shell wrapping the liquid metal droplet to implement mechanical compression to reconfigure its morphology, yielding an improved contact area for the polymer-metal junctions. The reconfiguration process produced a spatially uniform liquid metal array for interfacing with the printed top interconnects.”
A video shows the entire deposition process, and it well worth the two minutes it takes to watch.