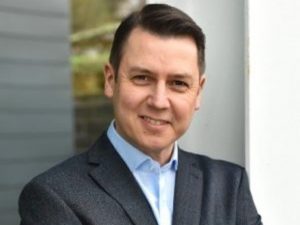
From simply reporting on the functioning of a die, on-chip monitoring has moved to dynamically adjusting a chip’s settings, to reporting how customers use the chip and even to influencing how end products are built.
This is why Moortec expects to treble in size from its current 50 headcount over the next three years.
“There is a monitoring revolution going on in the semiconductor industry and we are in a unique market position,” says Moortec CEO Steve Crosher (pictured), “we’re becoming a big player.”
So big that six out of the top ten semiconductor companies are Moortec clients.
“Effectively we can monitor anything on the chip,” says Crosher, “a lot of it is thermal sensing. We can see no one else doing this.”
Moortec’s unique market position grew from its ability to overcome a potential show-stopper for scaling – the phenomenon that power per unit of silicon area has been increasing for 20 years creating hot-spots and temperature gradients on a die.
Moortec’s technology distributes temperature sensors all over a die to monitor hot-spots and switch the chip off if it gets too hot – though there are better ways to do that now.
“We embed sensors in the design, the sensors are scattered throughout the die,” explains Crosher, “if the chip starts to ramp in temperature and goes above 100°C, the software can be instructed to slow the system clock rates and change the supply voltage levels.”
Dynamically scaling the voltage and the frequency obviously has less impact on a chip’s productivity than turning it off.
Conversely, of course, “if the chip’s running cool it can be instructed to speed up the frequency to get more performance,” says Crosher.
The key to doing this effectively is to have accurate temperature sensing. The more accurate the temperature sensing is, the closer the temperature threshold can be set to the limit which triggers the device being shut down or performance being throttled back. That enables maximum performance to be maintained for longer.
Accurate temperature sensing can have a dramatic effect on the end user. “By using super-accurate thermal sensors we can save money for the end user,” explains Crosher, “for every 1°C better accuracy you save $3 to $5 million for a datacentre over a year. We are making people aware of this.”
“With 40% of the electricity going into the data centre being spent on air-conditioning, if you can reduce the thermal levels of hardware, you can reduce the cost of ownership,” points out Crosher.
As might be expected for a company whose roots are in thermal management, datacentre is Moortec’s biggest market and automotive is a “close second” – both of them areas where controlling temperature is a primary challenge.
“In automotive the main consideration is reliability – there are extensive – 10-20 year – lifetimes for automotive, if you can tell how the chip is ageing we can make arrangements for when to swap it out,” says Crosher.
Predictive maintenance is a customer benefit of on-chip monitoring for other market segments as well as automotive.
After datacentre and automotive, Moortec’s main markets are networking high-performance computing and consumer. Currently the company is delivering 5nm finfet designs.
As monitoring grows in sophistication and scope, the quantity of data it throws up is edging Moortec into some surprising places.
“Once you’re getting data there’s a lot you could do with it especially over a long period of time,” says Crosher, “we do physical monitoring, thermal monitoring, process monitoring.”
“We are developing the ability to monitor conditions on a chip through the lifetime of a product and we can see how customers use the chip,” continues Crosher, “which is very interesting because it leads into analytics, and we can gather data across a whole product range and can see how a product range can be designed.”
This perception gives Moortec an open door to growth. It already has an international customer base: 40% of revenues come from China, 40% from the USA and 20% from RoW.
The coronavirus has had little impact on Moortec. “Q1 was very good,” says Crosher, “all the projects are rolling forward – with design cycles of two to three years it wipes out the effect of the coronavirus. A lot of the applications are in datacentre and telecommunications. Everyone is working from home.”